Press Releases
Metalwork and framing for fabric applications
Fabric is only half of the equation for many manufacturers in the specialty fabrics industry. The other half, metalwork and framing, requires its own set of capabilities.
A frame is the essential component that transforms fabric into architecture, turning a piece of cloth into some sort of protective cover or defined space. Generally made from aluminum or steel, frames provide fabric structures with shape, strength and flexibility.
But designing and fabricating metal framework requires different capabilities and skills than those needed to cut and sew the fabric that gets attached to them. The physical space alone presents a picture in contrasts—one workroom has saws, fire-breathing welding equipment, protective helmets and gloves, and an inventory of hard, sharp metal. The other has sewing machines, cutting tables and yards of fabric and thread.
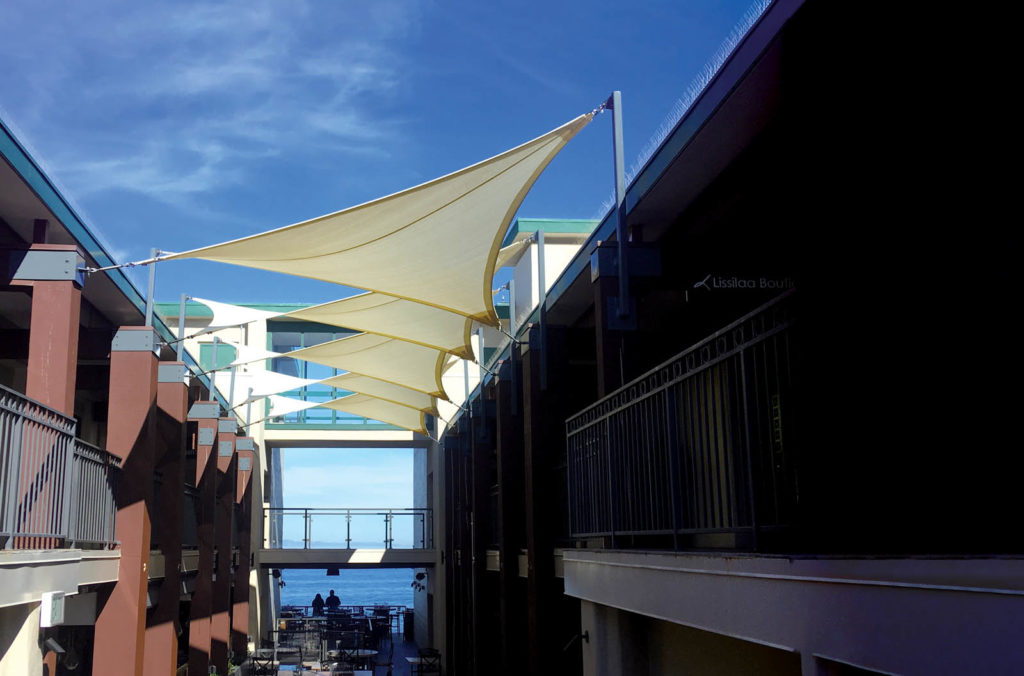
Some specialty fabric end product manufacturers contract with outside metal shops for their services. However, companies that perform metalworking in-house say that it makes them more competitive and efficient.
“If you want to be in the fabric structure or canopy business to any extent, you will need to metalwork to be competitive,” says Scott Neville, president of Kansas City Tent & Awning Co., Kansas City, Mo., and Welhener–H.B. Wall Awning, Ozark, Mo. The businesses produce fabric and metal awnings, canopies, shade structures, fabric signs and covers. Like many in the specialty fabrics industry, Neville says that having in-house metalworking capabilities allows his businesses to improve the bottom line by being more flexible, having better control over production schedules, and having more freedom to experiment with designs and techniques.
“Keeping all stages of fabrication in-house negates the need to mark up others’ effort,” Neville says. “Yes, there is a steep buy-in cost to do everything yourself, but it pays itself off soon enough.”
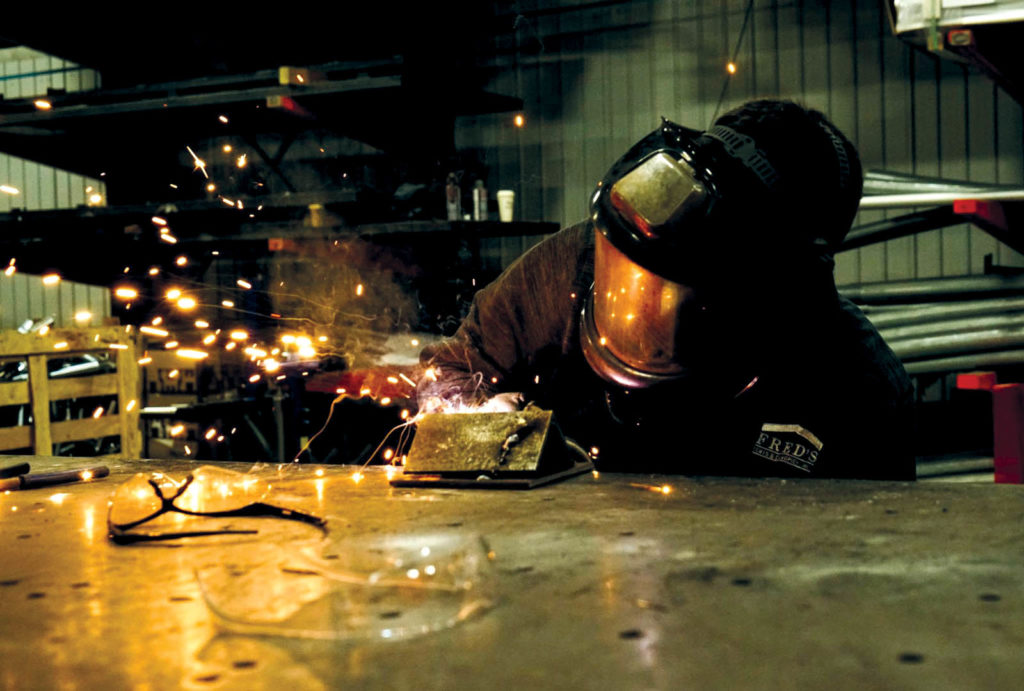
The fabric in fabrication
One of the major advantages of performing metalwork in-house is that the work will be done by people who understand fabric. Industrial textiles are more durable than ever, but they still don’t last forever. That fact plus the inherent pliability of fabric requires that manufacturers pay special attention to structural details to ensure the performance and competitive viability of fabric structures.
“Metal frames need to be fabricated by a knowledgeable fabric structure manufacturer. The finished look is dependent on a well-designed frame,” says Bryan Presby, principal of J. Miller Canvas LLC of Santa Ana, Calif., a custom commercial awning manufacturer serving the West Coast.
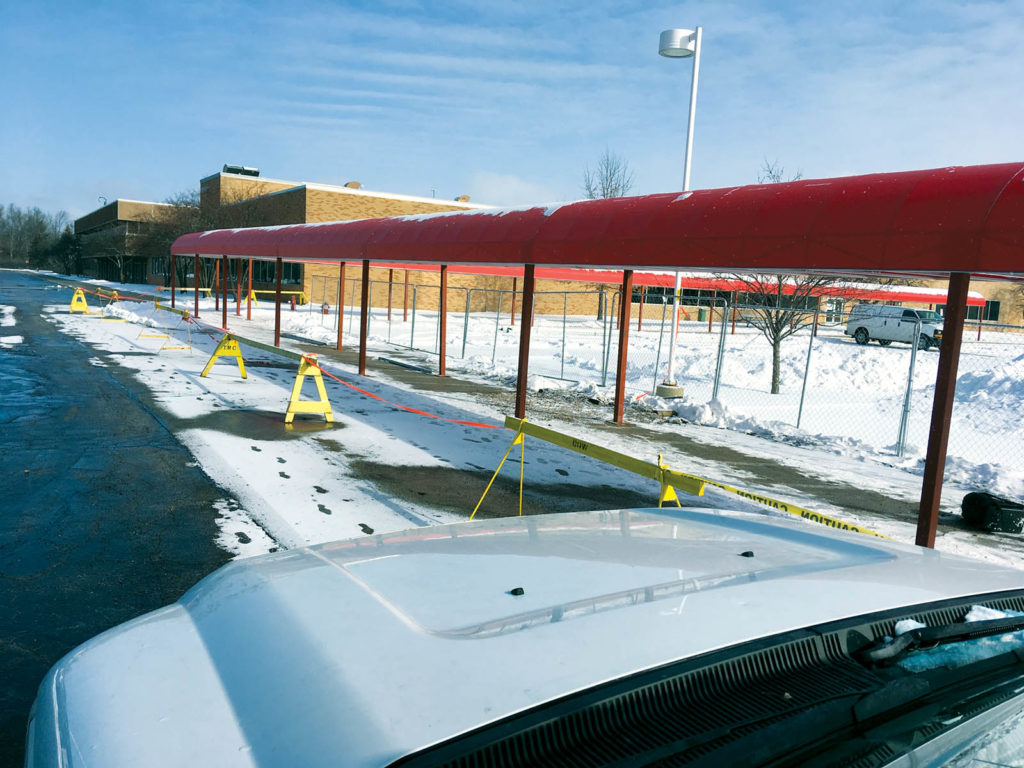
Using the right mounting and attachment hardware is also crucial to ensure a precise fit, so the textile looks sharp and functions as expected.
“If you’re making a metal structure to attach a piece of fabric to, it’s important that you carefully consider the attachment aspects and how it will perform on the structure and be easy to swap out when the time comes,” Neville says.
Accuracy and efficiency
Designing, fabricating and finishing metal frames requires a dedicated space, specialized equipment and skills, and a willingness to stay current with technology and trends. Muskegon Awning & Fabrication of Muskegon, Mich., has always done welding and metalwork in-house and continuously invests in the operation. The company has served western Michigan and the surrounding area for 130 years, originally by sewing feed bags and repairing horse harnesses, and today by manufacturing and installing fabric and metal awnings, covers and other specialty fabric products for residential and commercial customers.
“Lately, we’ve added more capabilities in order to create metal awnings, either a standing seam type or flat panel, which seem to be getting more popular,” says owner David Bayne. Bayne bought the company 15 years ago and added a showroom, Grand Rapids Awnings, in 2012. In the metal shop, Muskegon Awning uses both MIG and TIG welders and recently purchased a fully automatic push feed cut-off saw, which has allowed the shop to be more precise and efficient.
“The more accurate your cuts are, the better it welds; plus the welder doesn’t have to figure out how to cut it,” Bayne says. “And because it’s computerized, we can save it in the system and rerun it if the customer wants to order more down the road.”
Automation also means the company can handle large volume jobs, such as a recent project that called for 1,000 identical awnings.
Bayne points out that as much as Muskegon Awning tries to keep things in-house for cost-efficiency and quality control, it’s just as important to know when to send something out. Some shops also outsource finishing work, such as galvanizing and painting frames and components.
“We had a job for a thousand-foot walkway that required 5 tons of steel for support columns that we farmed out,” he says. “They’re heavy, and we didn’t want to mess with them in the shop while we were working on the canopy.”
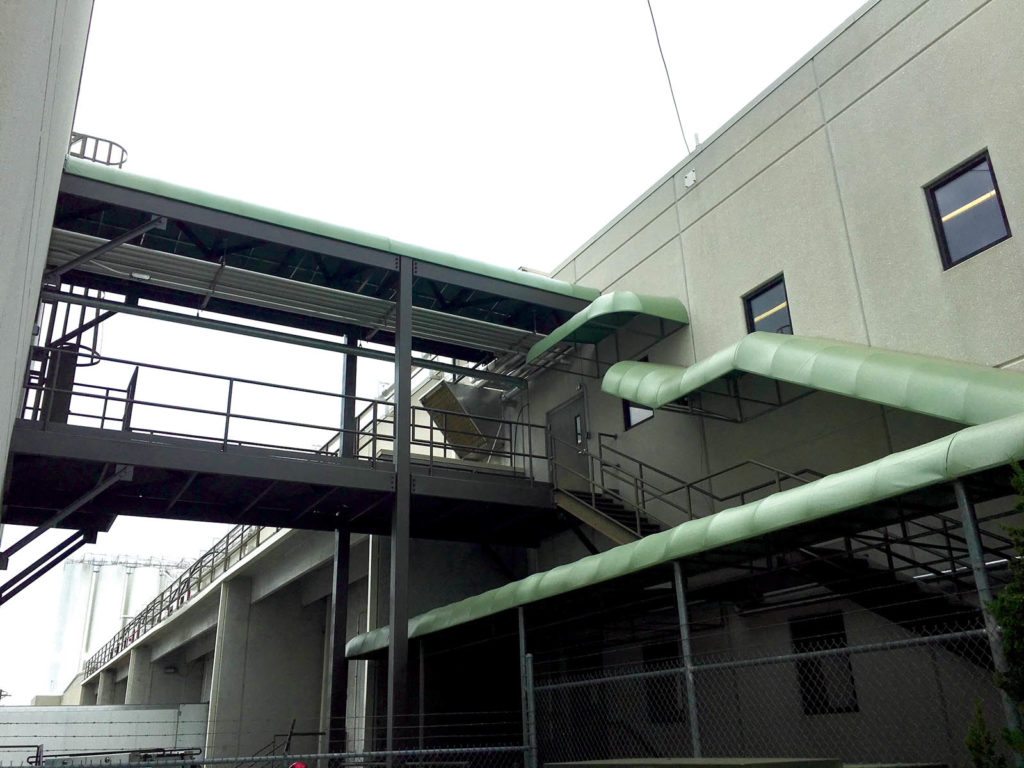
Skill acquisition
Fred’s Tents & Canopies Inc. prides itself on doing it all. The Waterford, N.Y.-based company has invested in equipment, staff and facilities to fabricate frames and parts in either aluminum or steel, including fittings and components, pole tent plates, tent masts, side poles, stake bars, door components, bent arches and ornamental details.
Although the company has always manufactured metal parts, the process of making those parts and pieces has changed significantly over the past 30 years, and exponentially over the last 10 years, according to Fred’s Tents president Fred Tracy. Tracy says that the investment in space and equipment has been worthwhile, but that there have been challenges, such as staffing.
“When you switch over to higher-tech machines, you need to think about the skills required to operate those machines,” he says. “For an employee that’s used to working a drill press, there’s often a learning curve associated with running
a CAD program on a CNC machine.”
Tracy recommends that businesses in the specialty fabrics industry look to vocational schools or community colleges to recruit employees and to equipment suppliers who may offer training for existing employees.
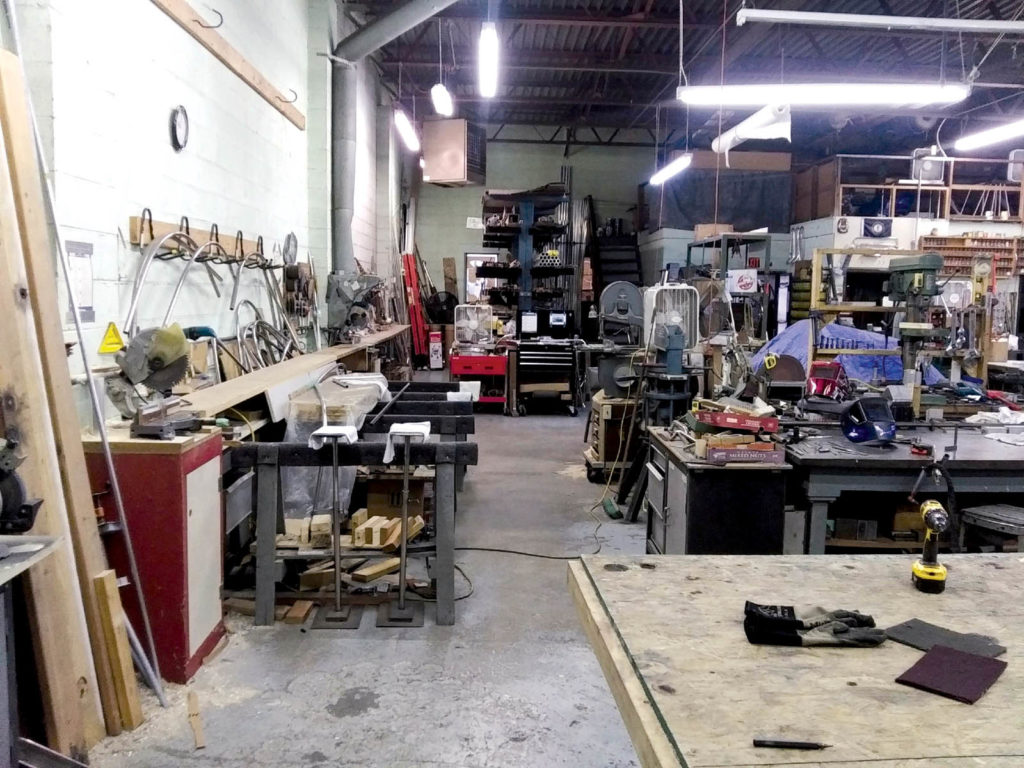
Go with the flow
Like any manufacturing process, metalwork requires examining a shop’s processes from beginning to end to get the full benefit of advanced metalworking machinery and eliminate redundancies and waste. In some cases, this means reengineering.
“Setting up your metalworking area is quite a process if you want the materials and product to flow through it efficiently and into the next step,” Neville says. “Both of our facilities are set up using the ‘lean manufacturing’ process.” Lean manufacturing is a systematic method of minimizing waste while maximizing productivity, thereby providing a higher value to the customer.
In other words, it’s not as easy as just adding one high-tech machine. To optimize performance when adding or upgrading equipment, a company needs to take the whole system into account. Advanced equipment is usually more precise than what it’s replacing; for example, machining to one-thousandth of an inch. Everything that comes before and after that step has to be more precise too.
“When equipment changes occur, the related prep, steps and finishing may also need to change,” Tracy says. “We purchased machines, but then the manual prep work couldn’t feed the machine fast enough. So we needed to upgrade that process as well.”
Doing it all
Sometimes the smartest way to add new capabilities and expertise to your specialty fabrics business is to buy an existing business. This was the case for Lake Shore Boat Top Co. Inc. of St. Clair Shores, Mich. In 2018 the company purchased Aquarius Marine Metal Products, a metal fabrication shop that Lake Shore had worked with frequently.
“They’ve been around since the early 1960s and had an excellent client base,” says Lake Shore owner Rob Kotowski. “Our goals with the purchase were to maintain their level of craft and service their customers with additional specialty fabric products.”
At the same time, Lake Shore decided to expand its prime location near Lake St. Clair along what’s known as “The Nautical Mile,” where there’s a high concentration of boats and marinas, to include a fully equipped metal facility while also maintaining Aquarius’s existing shop a few miles away. Despite early challenges—learning a new trade, equipment and processes; understanding an existing work culture; and retaining experienced workers—Kotowski says the investment has paid off.
“It’s been a good fit, and we have a lot to offer our customer base: frames, fittings, rails, welding applications,” he says. “You name it. We can now handle all of it.”
Laurie F. Junker is a freelance writer based in Minneapolis, Minn.
SIDEBAR: Buying in
Thinking about purchasing a metal shop to expand
your specialty fabrics capabilities? Here’s advice from
Rob Kotowski, owner of Lake Shore Boat Top Co. Inc.,
St. Clair Shores, Mich.:
- Do your homework to make sure the capabilities of your
current business and the new business are complementary
and that the workplace cultures line up. - Evaluate the metal shop’s equipment to determine
if it’s up to date or will need upgrading. - Consider your physical space. If your plan is to fold
the new business into an existing facility, do you
have adequate square footage? - Ensure that all stakeholders have the right mind-set.
“The biggest thing about buying an existing business
is being able to work with a new group of people and embrace
new ideas while still maintaining profitability,” he says.
SIDEBAR: Case study: Fred’s Garden Tent
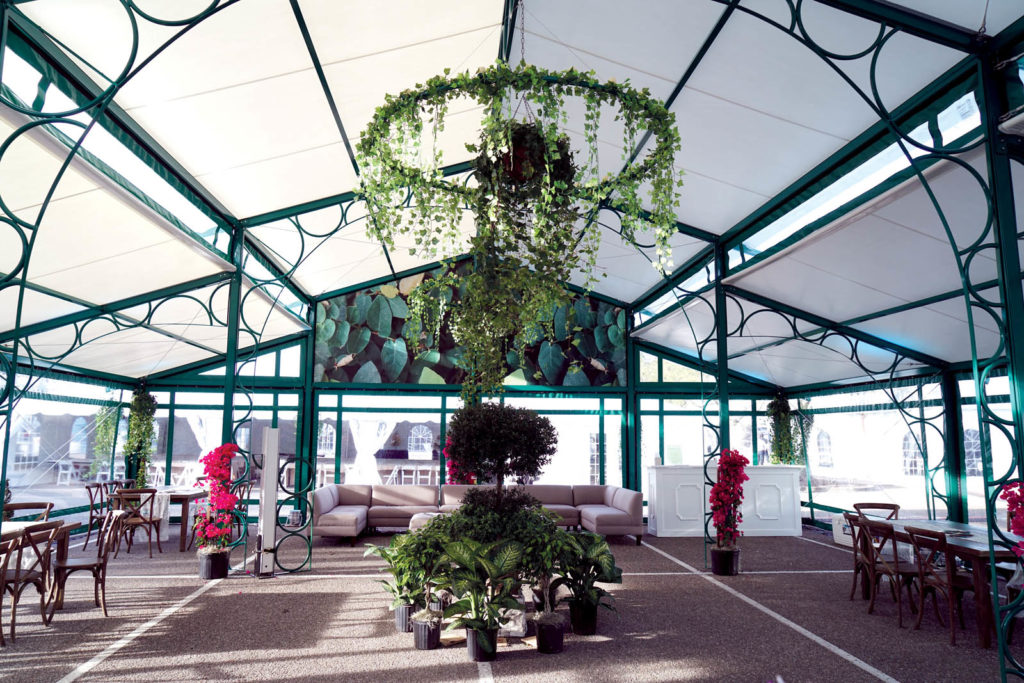
In 2018, Fred’s Tents & Canopies Inc., Waterford, N.Y., received a customer request to design and manufacture a garden tent inspired by the conservatory at Longwood Gardens in Kennett Square, Pa. The tent was unveiled at the 2019 IFAI Tent Expo in Orlando, Fla.
“Boy, was it a hit!” says Fred’s Tents president Fred Tracy. “The combination of the green metal framework, decorative rings and accenting fabric along with the flowers and plant displays brought our vision to life.”
The tent was possible because of the versatility of the shop’s ADD Extrusion, which allows the addition of ornamental decorations to any 120mm profile structure beam, including decorative pieces, hanging parts, fabric, lights and more. The company owns dozens of proprietary aluminum extrusion dies.
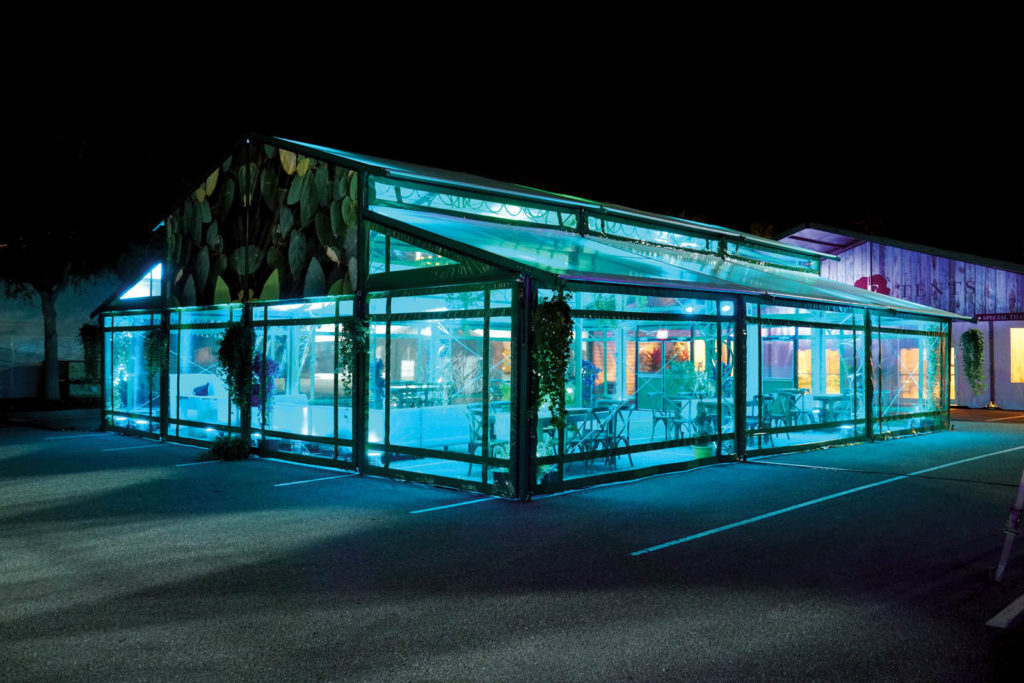
Other equipment used to create the Garden Tent included a roll bender on Fred’s BFS (Better Fabric Structure) line and a CNC machine for the milling and slotting of custom aluminum extrusions needed to attach the decorative parts to the ridgeline, rafters and legs.
“It was a challenge because of the different lengths, angles and heights,” Tracy says. “The circle design was ‘same but different,’ meaning although there were a few different arches, when it all came together, they had to look uniform.”
The design is also flexible—the decorative pieces are removable so the tent can be installed without them for use as a standard structure.
Read the original article at fabricarchitecturemag.com.